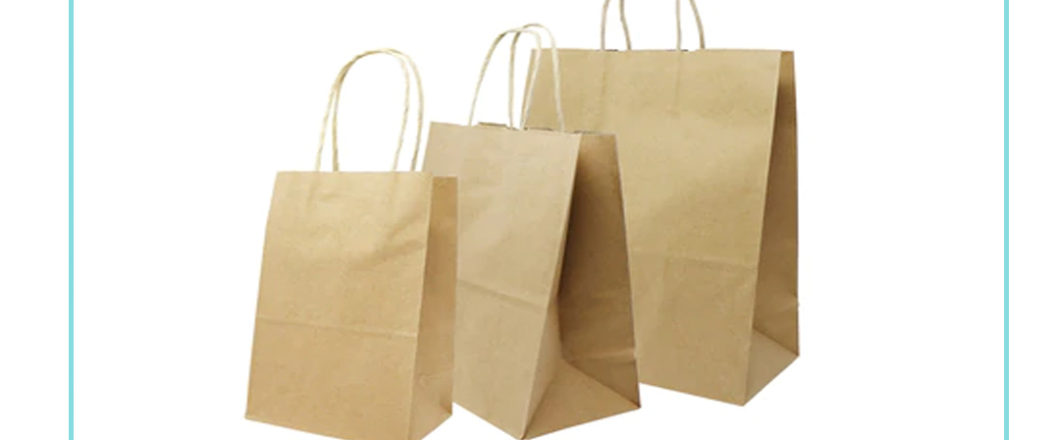
کاغذ بسته بندی نوع یونیون کرافت
برای آستر جعبه های چوبی به کار می رود و از دو ورق کاغذ خالص کرافت که با قیر طبیعی به هم چسبانده شده اند، درست می شود.
کاغذ بسته بندی نوع کرپ (یونیون زبر)
از دو ورق خالص کرافت زیر که به وسیله قیر طبیعی به هم چسبیده اند، درست شده است.
کاغذ بسته بندی یونیون زیر استحکام یافته
از دو کاغذ کرافت زیر شده تشکیل شده که یک لایه منسوج چتایی نیز به آن الصاق گردیده است؛ ماده چسبنده، قیر طبیعی است. این کاغذ از استحکام زیادی برخوردار می باشد.
کاغذ بسته بندی نوع یونیون کرافت زبر شده مقاوم به رطوبت
از یک ورق کاغذ کرافت خالص زبر شده، با یک ورق از جنس مشابه خود که در مقابل رطوبت دارای استحکام زیاد است و با قیر طبیعی به هم چسبیده شده اند، تهیه می شود.
کاغذ بسته بندی نوع یونیون زیر شده مقاوم به رطوبت
از یک ورق کاغذ کرافت زبر شده، با یک ورق از جنس مشابه خود که در مقابل رطوبت دارای استحکام زیاد است و با قیر طبیعی به هم چسبیده شده اند، تهیه می شود.
کاغذ بسته بندی پاتنت کنفی
از یک ورق قهوه ای و پایچه کنفی که با قیر طبیعی به هم چسبده اند، تشکیل شده است.
کاغذ بسته بندی کرافت با امولسیوت قطرانی
از یک ورق کاغذ از وع کرافت با امولسیون قیر طبیعی تشکیل شده است. هر یک از کاغذهای مذکور که با قیر طبیعی اندود شده اند را می توان بر اساس وزن پایه کاغذ، مقدار قیر و سایر متغیرها، تغییر داد.
مواد پر کننده
برای بهبود بعضی خواص از جمله کیفیت چاپ، براقیت (بهبود انعکاس نور) و ماتی، موادی به مقوا (لایه لاینر مقوا) و کاغذ بسته بندی اضافه می نمایند که فقط جنبه تبلیغاتی داشته و در بسته بندی کمتر استفاده می شود. مواد پرکننده مقاومت کاغذ و مقوا را کاهش می دهند. از مواد پرکننده معروف می توان به موارد زیر اشاره نمود:
- خاک رُس چینی
- سیلیکات مصنوعی
- سیلیکات طبیعی
- پودر تالک
- کربنات کلسیم
- سولفیت کلسیم
- سولفات کلسیم
- سولفات باریم
- سولفید روی
- دی اکسید تیتانیوم
اثر عوامل محیطی روی کاغذ و مقوا
عوامل محطیطی مهم و موثر بر بسته های مقوایی و کاغذی شامل رطوبت، دما، نور، گرد و غبار، عوامل میکروبیولوژیکی و بیولوژیکی، اسیدها و بازها می شوند.
رطوبت
با توجه به این که مقوا و کاغذ از الیاف چوبی تهیه شده اند و به لحاظ خاصیت جاذب رطوبت بودن چوب، بسته های ساخته شده از کاغذ و مقوا به مرور زمان رطوبت نسبی محیط را جذب نموده و با محیط اطراف به حالت تعادل می رسد.
در صورت عدم استفاده از آهار و مواد افزودنی ضد رطوبت، الیاف رطوبت را به خود جذب می نمایند، همچنین پیوند بین الیاف سست تر می شود.
در روطبت های بسیار بالا الیاف و لایه های کاغذ و مقوا از هم جدا و متلاشی می گردند. رطوبت مهم ترین عامل محیطی مخرب مقوا، کاغذ معمولی و فاقد آهار به شمار می رود.
دما
دما سبب خشک تر شدن الیاف می شود و اثر چندانی بر چسب و مقاومت کاغذ و مقوای کارتن ندارد (غیر از چسب های ترمو پلاستیک) ولی دمای بالا ممکن است سبب تغییر رنگ، قوس برداشتن مقوا، سوختن و به همراه رطوبت منجر به رشد عوامل بیولوژیکی و مخرب می شود.
نور
نور اگر سبب افزایش دما نشود، به تنهایی اثر چندانی روی کاغذ و مقوا نداشته و فقط ممکن است سبب تغییر رنگ ظاهری، سطحی و کم رنگ شدن علایم و تبلیغات چاپی روی آنها شود.
در صورت استافده از چسب، نور سبب ضعیف شدن بعضی از اتصال ها نیز می شود.
گرد و غبار
گرد و غبار ممکن است سبب سست شدن چسب های بین لایه ها و فرسایش سطحی کاغذ و مقوا شود؛ ولی به طور کلی اثر قابل توجهی بر آنها نمی گذارد.
عوامل میکروبیولوژیک، بیولوژیک و مخرب
شامل باکتری ها، قارچ ها و کپک ها، حشرات و جویندگان هستند که به طور مختصر هر یک را بررسی می کنیم:
باکتری ها: ممکن است کار تجزیه کاغذ و مقوا را بر عهده بگیرند. باکتری ها در هوا و خاک موجودند و همه چیز را آلوده می سازند این عوامل تا هنگامی که شرایط محیطی مناسب نباشد، هیچ ضرری نمی رسانند. پس از مساعد شدن محیط، رشد کرده و ازدیاد می یابند و مقوا و کاغذ بسته بندی یا کالا را می توانند مورد مصرف قرار داده و علاوه بر کاهش استقامت، سبب تولید مواد سمی و گازی نیز بشوند.
این گازها و مواد در بسته های کاغذی و مقوایی غالبا دی اکسید کربن و آب می باشند. گاز دی امسید کربن اغلب سبب پف بسته می شود و آب تولید شده برای بعضی از آنها در دمای بالای 60 درجه و پایین 4 درجه سانتی گراد نیز فعاعلیت هایی از خود نشان می دهند. اغلب بعد از تهیه بسته این عوامل کمتر مشکل ایجاد می کنند مگر آن که محیط نگهداری بسته ها بسیار نامساعد باشد.